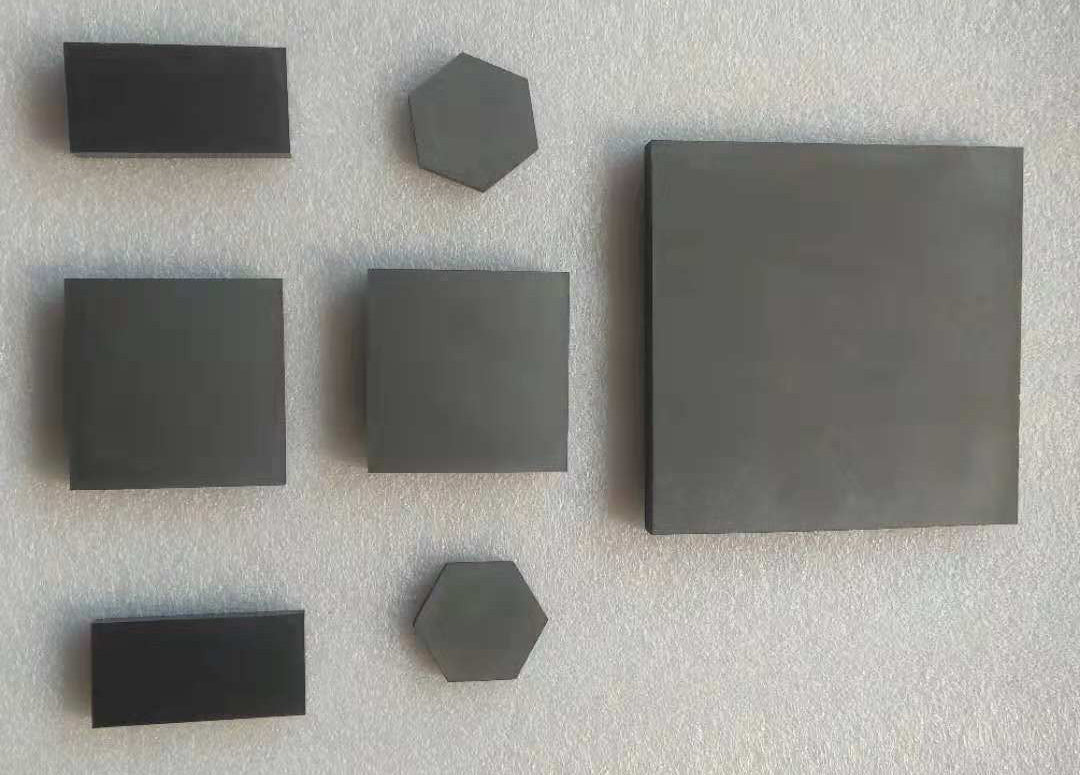
Next Gen Armor Ceramics: Beryllium Compounds
Share
Beryllium Boride
Be2B:
Density: 1.89 gm/cc
Hardness (Vickers): 1300 HV1
Fracture toughness: 2 MPa*m^1/2
Compressive strength: Not reported
There are three known, well-substantiated beryllium borides – beryllium-rich Be2B, and boron-rich BeB2 and BeB6.
The boron-rich compounds BeB6 and BeB2 are theoretical curiosities.
The hexaboride BeB6 has never been made or tested in ballistic experiments, and it’s expected to have properties similar to other XB6 hexaborides, which means that it should also be quite similar to boron carbide insofar as characteristics such as hardness and density are concerned. At least in those regards, it is expected to be unremarkable.
BeB2 has properties which are theoretically very interesting, but only studies on very small crystals – and in some cases wholly theoretical reports – have ever been published. As of 2024, the material has never been made as a bulk solid, and its real-world mechanical properties have never been tested.
The beryllium-rich Be2B, however, is no curiosity – it is an extensively tested ceramic material with remarkable properties.
In Wilkins’ LLNL “Light Armor Program” experiments, where more than two dozen ceramics were benchmarked against boron carbide, Be2B was also the best-performing armor ceramic by a wide margin. Indeed, it was the only one to out-perform boron carbide by a truly significant degree. This is plausibly due to its low density, combined with high compressive strength and resistance to bulk deformation.
In fact, Be2B is the lightest ceramic material to ever undergo ballistic testing, at just 1.89gm/cc. It is an extremely low-density ceramic.
Be2B has another interesting characteristic that makes it potentially valuable as an armor material: It melts at just 1520°C. (In comparison, B4C, SiC, and Al2O3 all melt at over 2000°C – over 2700°C in the case of SiC.) This means that it can be directly cast from a melt using industrial equipment made with common refractory materials. And, depending on its viscosity and certain other factors, it might be possible to cast it into highly complex geometries, such as helmet appliques. It might also be possible to use it as a matrix material in ceramic matrix composites – materials where strong fibers, whiskers, or platelets are embedded in a ceramic matrix. This can be done via conventional stir-casting techniques.
The LLNL group also reported the existence of another beryllium-boron compound, Be4B. At this point, however, it’s still unknown whether that constitutes a distinct ceramic compound or a solid solution of beryllium in Be2B. Very little has been written about it since the early 1970s, and it’s not considered well-substantiated. What we can say is that in comparison with Be2B it is slightly more dense, at 1.94 gm/cc, has ballistic performance that’s slightly worse, and that it has a substantially lower melting point, at 1160°C – which is uncommonly low for a ceramic. (Though not totally unprecedented. MgB2 also decomposes/melts at a relatively low temperature.)
So far, so good. So why is nobody using beryllium ceramics in armor?
Well, as it turns out, beryllium is among the most toxic non-radioactive elements, right up there with arsenic and thallium. Inhalation of beryllium dust – and this includes the dust of beryllium compounds like BeO, Be2B, etc. – can be deadly toxic, even in very small amounts. It’s not a pleasant or swift death, either.
There’s an old science fiction story by Issac Asimov – “Sucker Bait” – about a large group of interplanetary colonists who settle on a distant world. A mysterious illness kills every last one of them. Only later is it discovered that the planet’s crust had an unusually high concentration of beryllium compounds. Which sounds about right, as beryllium dust is not the sort of thing that you can detect with a geiger counter, it’s not especially toxic to plant life, and it kills in a slow way that’s hard to attribute to poisoning – it can look more like a respiratory disease.
Granted, it is at present unknown whether all humans are susceptible to beryllium toxicity, or whether it’s something that only affects people who are particularly sensitive due to genetics or environmental factors. It has been reported that different variants in the gene HLA-DPB1 may confer either resistance or heightened susceptibility to beryllium toxicity. This is largely academic; as with other highly allergenic agents, it’s likely that repeat exposure is associated with sensitization, and nobody wants to risk exposure.
So beryllium has very few industrial uses. In descending order of importance: (1) In beryllium-copper tools containing 2% beryllium or less, as beryllium strongly strengthens copper and beryllium-copper doesn’t spark upon impact. (2) In niche, high-end aerospace beryllium-aluminum superalloys, which take advantage of beryllium’s stiffness. (3) In antique or very high-end audio equipment that takes advantage of its extremely high sonic velocity and good acoustic properties. (4) In X-Ray machines and in various applications that take advantage of its transparency to X-ray wavelengths. (5) In heatsinks that take advantage of BeO’s good thermal conductivity combined with the fact that, unlike copper, it’s an electrical insulator.
Wherever beryllium is used, there are efforts underway to try and replace it with something else. BeO heatsinks and beryllium speaker cones are already almost totally obsolete.
Though not a rare element in the Earth’s crust, beryllium has so few industrial uses and is so dangerous to handle that it is produced only in very small amounts. Total global production of beryllium metal and beryllium oxide ceramics is on the order of ~330 tons per year. To put this into perspective, global production of silicon carbide currently stands at roughly 2 million tons per year, and alumina is produced in quantities of over 140M tons per year!
Something so scarce and so toxic is bound to be expensive, and indeed it is. A beryllium boride (Be2B) torso armor plate would cost well over $4000 per unit. This is partly on account of the raw material cost, and partly on account of the precautions and safety measures that need to be taken during production. Such a plate may also pose a hazard to its wearer: You get shot, your Be2B-faced armor plate stops the threat – but you’re shocked, breathing heavy, and your lungs absorb a large enough amount of atomized beryllium compounds to poison you in the weeks or months which follow this first brush with death. A dark scenario; the sort of thing product liability lawyers feed upon.
Though the focus of this post has been on borides, there is also a beryllium carbide, Be2C. This, like Be4B, is still relatively mysterious. Most of the research into this carbide was done in the 1950s, and there has been remarkably little work on it since then. It appeared to have attractive properties – very low density, high hardness, high stiffness – but the samples tested in those days were either highly porous or highly impure, so it’s difficult to say for certain how it might perform as a high-quality dense ceramic part. The greater difficulty, however, lies in the fact that Be2C is unstable in moist air, and decomposes to give methane. So it’s doubly unsuitable as an armor or engineering material: Not only highly toxic, but also unstable under normal ambient conditions.
It appears that beryllium compounds have no future in armor, but there are other next-gen compounds that have potential, and Vstone is working hard at bringing them into the light of day. Ceramics derived from other light elements – silicon, magnesium, and others – have untapped potential. More will be written about this later.